The impact mill has been specially designed for breaking up agglomerated material within the bulk product. This application is mainly used in the treatment of boiler ash originating from incineration plants. The adjustable impactor reduces the bulk material’s size to a degree of granulation suitable for pneumatic conveyance. This is indispensable in order to ensure a high level of functional safety in pneumatic conveyance, even for critical bulk products.
The bulk material is fed into the rotor by means of a slide. The impactor is composed of two static, adjustable baffle plates. The beaters at the rotor project the bulk material against the baffle plates. This operation is repeated until the bulk material’s grain size is smaller than the distance between the beaters and the baffle plates. The use of an impact mill allows to modify the whole range of grain sizes.
Experience
- > 150 mounted impact mills
- Modular construction - may be upgraded with coarse sieve
Special Characteristics – Application (USP)
- Bypass for fine particles
- Solid welded housing
- Hinged housing provides for easy maintenance
- Amour-plated housing fitted with interchangeable wear plates
- Shaft sealed by means of labyrinth-seal and flushing gas
- Adjustable impact mechanism for final grain size
- STAG Service Support
Industries
- Waste to Energy
- Cement industry
- Steel plants
- and many more
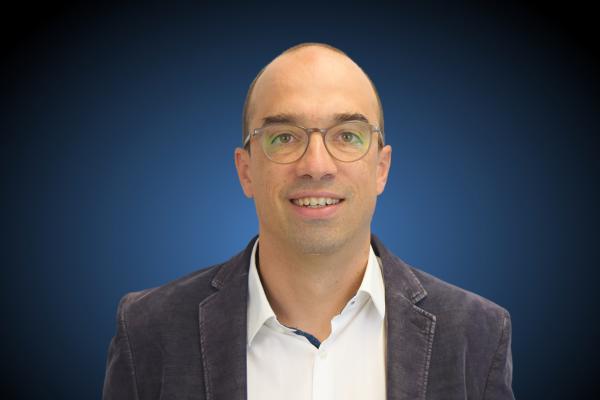
- Temperature resistance up to 300°C
- Flow rate 15 m3/h (product-specific)
The pressure conveying vessel is used by STAG when it comes to challenging tasks, high conveying rates and long con-veying distances. This pneumatic conveying application using the dense flow method combines energy-optimised conveying processes with perfect operational safety.
Based on their long cooperation in the area of conveying systems for thermal waste treatment plants, Hitachi Zosen Inova and STAG have already realised several projects together. In 2015, a completely new waste treatment plant featuring two lines has been put into operation in Perlen (CH).
In the waste-to-energy power plant Hagenholz, the overall bulk material handling in the area of boiler and flue gas cleaning, ash washing as well as dry slagging has been installed by STAG.