Chain conveyor are continuous conveyors and are suited for the conveyance of bulk products of all kind up to small-sized products and sludges. The advantages are its excellent temperature resistance (up to 800°C), the low conveying velocities, particularly in case of abrasive bulk material, and the robust and dustproof design. There is a wide range of possible applications and different configurations. At present, more than 300 devices are used by more than 70 customers worldwide.
Experience
- > 300 chain conveyors built
- > 40 pcs. in the temperature range over 600°C
- > 30 pcs. presenting sloped or inclined sections
Special Characteristics – Application (USP)
- Automatic thermal expansion compensation thanks to chain slack construction
- Integrated tensioning station for wear compensation
- Low-wear design in the high-temperature range
- Exterior dustproof and pressure-resistant flange bearings
- Customer-specific detailed solutions (Obertrum)
- Special discharge conveyors designed for boilers 2/3 Zug MVA
- STAG Service Support
Industries
- Waste-to-energy power plants, thermal waste treatment
- Energy generation and power plant industry
- Cement industry, mineral and constructions materials
- Waste water, sewage sludge and Recycling
- Steel industry
- Numerous customized solutions
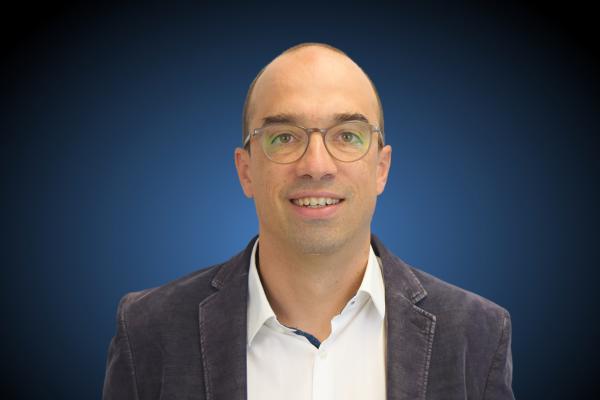
• Conveying lengths 6 - 50 m
• Conveying heights 3 - 35 m
• Conveying rates 1 - 100 m³/h
• Dimensions (width) 290 bis 1100 mm
• Temperature resistance up to 800°C
- Waste-to-energy power plants, thermal waste treatment
- Boiler, electric filter and fabric filter ash removal
- Slag discharge
- etc.
- Energy generation and power plant industry
- Electric filter ash removal
- etc.
- Cement industry, mineral and construction materials
- Animal meal
- Cement
- Sewage sludge
- EBS
- etc.
- Waste water, sewage sludge and recycling
- Sewage sludge wet and dry
- Bunker discharge
- Steel industry
- Numerous special solutions
In this diesel-fired power plant, exhaust air is cleaned by means of two electric filters. Respectively two trough chain conveyors per filter serve for evacuating the ash. For each line, a collecting trough chain conveyor is provided receiving the ash.
The closed STAG Conveyor Belt stands out through its dustproof design and its integrated scraper floor. With this construction method the conveyor belt can be operated by a slight vacuum.
In 2013, a modern coal block has been put into operation in Karlsruhe. For this project, STAG was entrusted with the engineering and delivery of the mechanical and pneumatic ash removal of the electric filter.