In conventional conveyances of powdered bulk materials through smooth pipes, the irregularity of the flow rises with the increasing pipe length. This in turn, increases the wear of the system.
The use of the STAG DenseFlow conveying line system represents a more advantageous solution in terms of technology and profitability in order to resolve the described irregularity of flow. In the upper part of the conveying line, this system is provided with a secondary line with apertures; thanks to this construction design, any pipe congestions are prevented and/or removed.
Moreover, the wear of pipes is substantially lower in a STAG DenseFlow system due to the low conveying speed. From the comparison of the mean conveying velocities it appears that the STAG dense phase plant with DenseFlow conveying line system operates at about half the conveying speed of a conventional pressure conveying system fitted with smooth pipes.
Experiences
- More than 100 installed conveying lines
- 6‘000 m in total
Special Characteristics – Application (USP)
- Low wear
- Easily retrofittable
- Energy-optimised
Industries
- Power plants
- Steel plants
- Construction materials industry
- Paper industry
- etc.
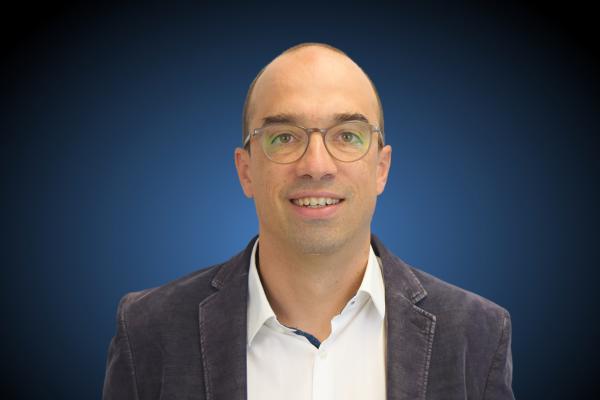
The pressure conveying vessel is used by STAG when it comes to challenging tasks, high conveying rates and long con-veying distances. This pneumatic conveying application using the dense flow method combines energy-optimised conveying processes with perfect operational safety.
Injector:
Injectors are used for the simple, self-regulating in-feed of powdered and granular bulk products into pneumatic conveying lines without moving parts.
In 2006, STAG received the contract of Fisia Babcock Environment GmbH to equip the lignite-fired power plant (BOA ll - RWE) in Neurath, Germany, with pneumatic conveying facilities designed for the ash removal of electric filters.