STAG’s container handling system enables automated and dust-tight filling of roll-off containers. The
container is tilted with the traversing and tilting station, thus achieving an ideal filling level.
STAG can develop a targeted concept for customer-specific operating requirements. With additional
options such as reversible filling conveyor belts, feed hoppers and docking chutes with integrated
filling flaps, many systems are successfully in use.
Automated tipping station with lowering and lifting hydraulics for filling specially developed ACT containers for the bulk material dry slag. The container is pushed onto the frame by the truck with hook or chain equipment as far as it will go and tipped hydraulically.
The filling process is then started and when it is finished, the container is lowered again and picked up by the truck.
The design is based on the drawings and documents prepared by STAG. The tilting table is designed as a stable welded sheet metal construction. It essentially consists of a lower frame section, middle section and the tilting frame. In addition, 3 fixings with spherical bearings, 4 side guides, consoles and locking devices as well as stops are provided. A 6-stage telescopic cylinder serves as the tilting device. A locking cylinder and a cylinder for the tiltable stop are also fitted.
Experience
- 2 redundant filling systems at ERZ Hagenholz
- 1 pc. Emptying station at KEZO Hinwil
- 1 pc. Filling system at KEZO Hinwil
- 1 pc. Filling system at KVA Horgen
- 1 pc. Filling system at Satom Monthey
- 2 pcs. Filling systems at Enova Zuchwil
USPs
- Clodes design, dust.tight
- Self-cleaning due to scraper fllor
Industries
- Waste to Engergy plants - Slag handling
- Steel industry
- Cement industry
- and many more
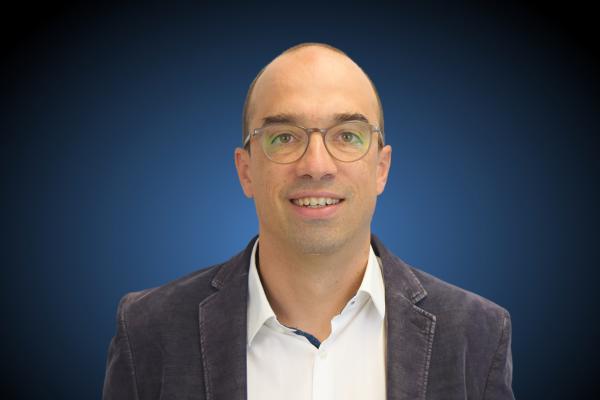
The closed STAG Conveyor Belt stands out through its dustproof design and its integrated scraper floor. With this construction method the conveyor belt can be operated by a slight vacuum.
Coarse particle separators are used in mechanical conveying processes of bulk products in order to eliminate larger particles (impurities). The benefits are an improved operational safety of the conveying system, which can be reduced in size after the coarse particle separator.
We are happy to carry out the necessary revision of replaced machine components. Send us your aggregate to Maienfeld and we will inspect and revise it. Experienced mechanics and plant and apparatus engineers inspect the unit.